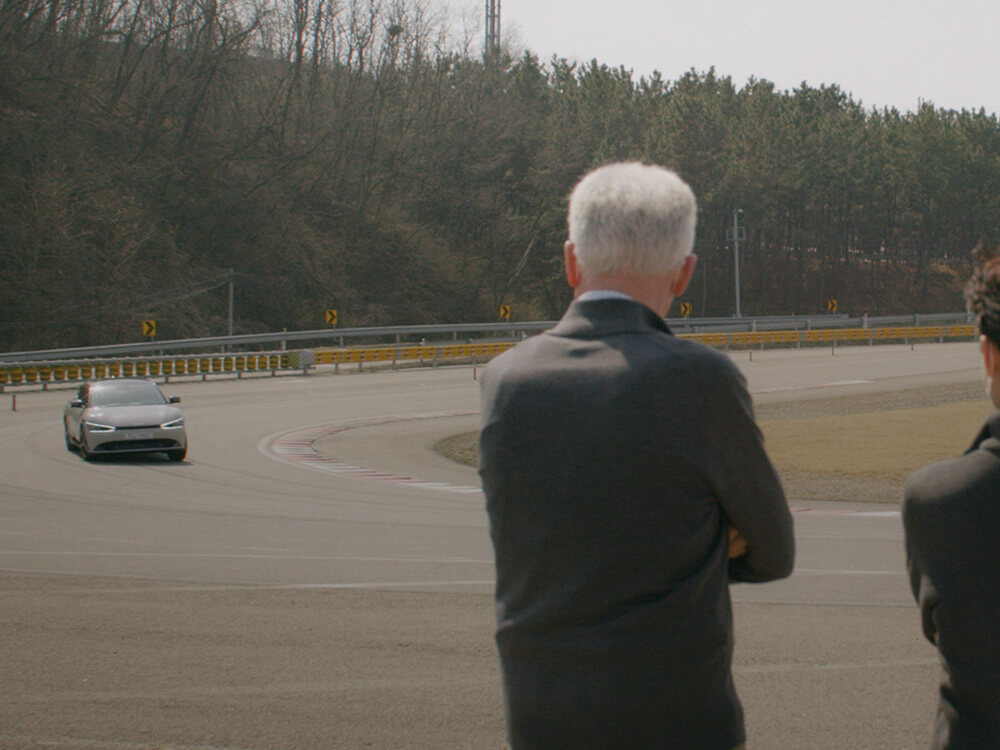
Safety & Health
Safe Workplace, Healthier employees
Establishment of Safety Management System
Kia is building a safety management system based on ISO 45001, using the principles and policies of safety and environment as its foundation. With the goal of establishing autonomous safety management, we have set the Safety and Environment Vision 2025 Roadmap to achieve a safety and environment system at the level of ‘voluntary participation.’ Accordingly, we are promoting improvement activities.
Mission
By putting people and the environment first, we strive to create a culture of safety and make it a part of out daily lives.
Vision
Integrate the safety and environment systems of all our facilities across the globe and achieve Safety Level 4 by 2025.
Safety and environment management system
Proactive regulatory compliance
Meet global requirements and minimize regulatory risks
Inherent safety design
Ensure perfect safety from the design stage
Minimize environmental pollutant emissions
Actively adopt energy-saving and eco-friendly technologies
Internalize safety consciousness
Promote a culture of complaance and establish a safety education system
Basic Principles
Mid- to Long-Term Directions for Ensuring Security
Year | ~2020 | 2021~2022 | 2023~2024 | 2025~ *New Targets To Be Set After 2026 |
---|---|---|---|---|
Target | Safety leadership | Manager-led safety management | On-site participatory safety management | Establishment of autonomous safety management |
Culture |
|
|
|
|
System |
|
|
|
|
Workspace Environment |
|
|
|
|
Safety and Environment Policy
1. Compliance with laws and regulations related to the safe environment
We have a safe environment system that meets global requirements, comply laws and regulations, and prioritize the requirements of stakeholders.
2. Minimization of the risks of the safety environment
We build a safe and pleasant work environment where our employees can create the value of their work and provide a happy experience to customers.
3. Minimization of environmental pollutant emissions
We optimize energy and resource input in all production areas, and actively introduce ecofriendly technologies to minimize emission of environmental pollutants.
4. Organizational culture in which safety is internalized
We strive to create a safety culture in which employees discover threats and proactively address those threats in order to create a safer workplace.
Kia Safety and Environment management system
Kia prevents industrial accidents by providing a safe and pleasant work environment and spreading a safety culture, and improves the health of its and its partners' employees to fulfill its corporate social responsibility. We realize safety and health sustainable management by establishing an autonomous safety management system based on the safety and health management system (ISO) with the support of the safety and health leadership of the top management.
Industrial Accidents
2022 | 2023 | 2024 | |
---|---|---|---|
No. of industrial accidents | 388 | 457 | 381 |
Industrial accident rate(%) | 0.77 | 0.89 | 0.75 |
Lost Time Injury Frequency Rate(LTIFR*)
Classification | 2022 | 2023 | 2024 |
---|---|---|---|
Employees | 1.71 | 1.82 | 1.36 |
Suppliers' employees | 16.53 | 10.76 | 14.59 |
* LTIFR : Loss of work accident rate, and the formula is as follows: Number of injuries (accidents) in a 12-month period / Total hours worked by all employees in the same 12-month period x 1,000,00
Occupational Injury Frequency Rate(OIFR*)
Classification | 2022 | 2023 | 2024 |
---|---|---|---|
Employees | 2.15 | 2.65 | 2.40 |
* OIFR : Loss of disease-related accident rate, and the formula is as follows: Number of injuries (accidents) in a 12-month period / Total hours worked by all employees in the same 12-month period x 1,000,00
Serious Accident Prevention
Critical Accident Reporting System*
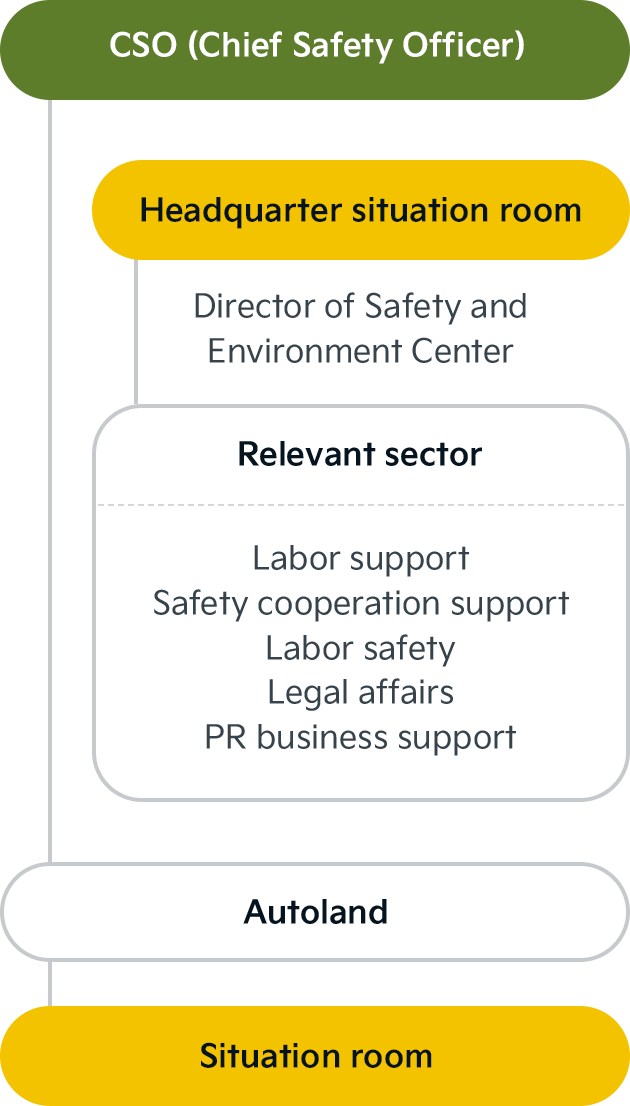
CSO (Chief Safety Officer)
Headquarter situation room: Director of Safety and Environment CenterRelevant sector: Labor support, Safety cooperation support, Labor safety, Legal affairs, PR business support
Autoland Situation room
* Autoland
Main Task
- Initial Response - Suspension of work, evacuation of workers, measures to prevent further damage
- Accident investigation and accident report (internal/external)
- Patient status identification and relief measures
Critical Accident Prevention System
- Regular operation of company-wide safety review meetings led by the Chief Safety Officer (CSO)
- Sharing and supporting SIF discovery and improvements 3 times a month - Creation of a Serious Accident Prevention Team
- Inspection and report on the implementation of the Serious Accident Punishment Act
- Review of safety and health compliance and reporting to the CSO once semiannually - Activation of Serious Accident Contingency Plan and conducting regular drills (once semiannually), etc.